
Sign In
Sealing an Anti-Air Warfare Destroyer
05-10-2015
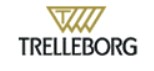
On the eve of the scheduled launch of the fi
rst of the Royal Navy's Type 45 Daring Class Anti-Air Warfare Destroyer, MER takes
a detailed look at the composit
e bearing materials specified onboard
The Type 45 Anti-Air Warfare Destroyer will provide air
defence cover for the Royal Navy and will replace the Type 42
destroyers in service.
The deep displacement is circa 7350t with a length of 152.4m and a beam of 21.2m.
The water Iubricated shaft bearings comprise the Main 'A'
Bracket bearings and Intermediate bearings. Port and starboard
shafts are of different lengths.
Because the shaft loading geometry has a
large variance between the cold (static)
condition and the warm (MCR) condition
together with the length of the 'A' Bracket Barrel a computer program was developed to assess the bearing loading under both
conditions.
The shaft bearings are required to operate at extremely low shaft
revolutions and therefore cannot rely on the hydrodynamic lif
t
induced by the shaft rotation; Orkot TXMM was selected as this
material has low friction under
boundary lubricated conditions.
The other requirements were that the bronze bearing housing shoul
d remain fitted in the bracket barrel under refit and that the
bearings should be capable of
being removed without dry-docking in an emergency.
Three segments
The bearings are in three segments with the bottom segment
forming a 140deg arc, for good hydrodynamic performance. The
bearing pressure was limited to around 5.5 bar but in reality this
will vary due to the variable shaft angle from cold to MCR.
The segments are locked in position with a removable key asse
mbly which is easily accessed with the front retaining ring
removed. The key can be withdrawn as a self-contai
ned assembly allowing each segment to be removed.
The bearing segments are machine-finished, which removes
the need for any machining or work in the shipyard.
The Main 'A' bracket bottom segment is designed from the com
puter program to allow for elastic deformation. This eases
bedding in by increasing the contact footprint and reducing the
edge loading, because the shaft angl
e changes from positive to
negative from static to MCR.
A
s the aft bracket barrel is longer than required for bearing requi
rements, and to reduce the effects of the shaft angle, the
forward third of the bearing length is relieved as a safety bearing.
One requirement for the intermediate bearing is that the pr
opulsion shaft has to be removed at an angle and therefore the
bronze housing has two location diameters with the smaller diamet
er fitted into a removable bronze housing at the other end of
the barrel. This allows the shaft to be tilted for removal within the length of the vessel.
Both the intermediate and aft bearings were fitted with thermo
couples to monitor the bearing
surface temperature during the
basin trials. The reason is that for these
trials the resistance to the propulsion moto
r is by brake blades fitted in place of
the
normal propeller blades. Since brake blades
do not induce thrust there is no propeller lift to reduce the bearing pressure.
For any water lubricated bearing a period of running in is requi
red to form the optimum running surface for hydrodynamic
operation. As crude torque measurements are not sufficient
to determine when the bearing is operating in this mode,
thermocouples were fitted into the bearing
to moiiltor bearing surface temperature.
Coupling protection
The shaft protection covers are designed to protect the hydrau
lic coupling which joins the propulsion shafts together from
seawater corrosion.
Corrosion on the coupling nut and taper sleev
e can prevent the normal disassembly of the coupling on refit and severe
corrosion on the body of the coupling will reduce the hoop Stress induced by the taper sleeve.
Prior to this, aluminium cones and rubberi
sed protective coverings were used. T
he effects of the shaft torque can cause
cracking at the cone interfaces allowing seawater to penetrate
into the coupling causing co
rrosion on the aluminium cones and
coupling faces. The internal voids in
the cones were filled with tallow.
Orkot Marine Bearings redesigned the complete covering system
using their machinable composit
e material. This allows the
coupling to be completely covered and sealed without the us
e of epoxy bandage, rubberised c
oatings and aluminium cones.
The Type 45 Coupling protection covers were purpose designed to
suit the exacting requirements for this vessel. This was more
difficult due to the proximity of the ropeguards (also manufacture
d from Orkot machinable composites). They comprise of a
machined sleeve which covers the coupling
to which cones are fitted and sealed with
o-rings. The cones are located axially on
the shaft with a split ring which is bonded to the bronze liner.
The other end of the sleeve is fitted with a short split cone.
Both cones clamp onto the shaft
and liner to prevent rotation.
Trelleborg Orkot Composites use a spec
ially developed biodegradable grease which is
pumped into the internal voids of the
coupling after assembly to further protect the coupling.
Both the intermediate (pictured
above) and aft bearings were fitted
with thermocouples to monitor the
bearing surface temperature
during the basin trials
A
typical ropeguard and coupling cover
after docking, shown here on HMS
Westminster (Courtesy UK MoD)
Rudder stresses
The Type 45 vessel in common, with most Naval vessels, uses
a spade type rudder. This type of rudder imparts higher
compressive stresses to the bearing as the rudder is unsupport
ed. This could subject the bear
ing to unequal bearing pressures
if a stiff bearing was used, commonly known as edge loading.
Normally Naval rudder bearings are grease or
oil lubricated. This is essential if they
are manufactured from corrosion resistan
t
steels or bronze materials as these woul
d suffer from 'pick up' (contact transfer
of bearing material to the shaft).
Unless these bearings are adequately sealed, oil or grease
could leak into the seawat
er which would be unsuitable
environmentally or for traceability.
It was decided to use seawater injection into the bearings as
it was considered too large a step to operate totally dry.
Orkot TXMM was selected for its low friction under dry operation,
low static to dynamic friction
(stick slip) c
ontrolled elasti
city
under dynamic loading (hysterisis).
When the bearing is dynamically loaded under unequal loading (bendi
ng or misalignment) the material deforms elastically to
give a larger contact area.
This reduces the unit bearing pressure. The recommended maxi
mum static pressure will be between 80-100N/mm2, this being
the elastic limit for this material. It is incorrect to cons
ider the maximum compressive
strength (>280n/mm2) as plastic
deformation occurs above the elastic lim
it without full elastic recovery.
If a metal bearing is subjected to the sa
me loading because the material is much
stiffer, the loaded area is smaller (edge
loading); this can cause damage betw
een shaft and bearing i.e. metal transfer, hence t
he use of oils or greases to help reduce
metal to metal contact.
The bearings as fitted to the Type 45
are retained using the bearing interferenc
e designed using the company's bespoke
calculation program. This calculates
the required bearing retention under all
operating conditions, including the maximum
turning force (torque) developed from t
he friction force between shaft and bearing, the operating temperature, and the
machining temperature. If the bearing is overstressed i.e. from
elastic to plastic deformation,
it could loosen and turn in the
housing blocking the water feed holes.
When Orkot TXMM operates dry, the bearing lubrication comes from
the transfer of lubricant from bearing to shaft, further
reducing friction and wear. Normally the higher
the bearing pressure the lower the friction.
Fin stabiliser bearings
It was decided that due to Orkot TLMM's dry operational capability
and lower wear, it should be used on the Type 45 Destroyer
Fin stabiliser outer bearing. These are lubricated directly from
the seawater via the axial grooves, and if any water blockage
occurs the bearing will still operate. These bearings are subjec
t to reciprocating operation with bearing pressures up to
25N/mm2. The bearings can be removed and replaced under wa
ter using purpose designed habita
ts – a well proven operation.
For more information on Sealing an Anti-Air Warfare Destroyer talk to Trelleborg
Enquire Now
List your company on FindTheNeedle.