
Sign In
Maintenance expertise, built in
01-07-2021
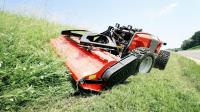
It’s fair to say that no one knows their machines as well as the manufacturer. Yet this close technical relationship is often lost when a machine is sold via a dealership network. This means that technical expertise is distanced from the customer and can result in a complicated chain of communication.
However, thanks to our IoT offering, BODAS Connect, machinery can be monitored remotely and kept in optimum operating condition much more easily.
Machine manufacturer, REFORM, is a well-established supplier of agricultural and municipal vehicles. REFORM understands that the search for solutions to maintenance issues can lead customers down a complicated path – including the risk that the first point of contact in case of issues can become a negative experience.
Closing the gap
Typically, in case of an issue with a machine, customers contact their local dealer for diagnosis. If the dealer is unable to provide an acceptable solution, the issue is eventually passed on to the machine manufacturer. REFORM recognized this process can be shortened and converted from a negative touch point to a positive experience. Whilst every measure is taken to ensure help and support is received as quickly as possible, this traditional process is both costly and time consuming because multiple parties are involved and machine information needs to be communicated. With connected machines, it’s now possible to make machine information and issues transparent to all involved parties (dealer and manufacturer) at any point in time.
Connecting manufacturers with machines
We’ve had a strong working relationship with REFORM for many years, so we were the obvious choice to become their partner in this step towards digital transformation. Our BODAS Connect solution was chosen to connect REFORM to its vehicles and customers through three key elements:
The Connectivity Unit that’s installed in each vehicle
The web portal that displays and visualizes the machine data
The Bosch IoT Suite with its underlying cloud-infrastructure, acting as an analysis platform.
Innovation in the field
The new technology is already being used by REFORM in the development of its latest prototypes. This will enable the company to offer future customers connected machinery that can be monitored remotely and kept in optimum operating condition.
Simplifying machine maintenance
Most of the relevant maintenance issues can be identified early on and effectively resolved with minimum downtime. A further step towards simplifying operations is the ability to remotely update machine software “over the air” in order to fix any software issues or improve performance for a whole fleet.
For REFORM’s customers, this solution simplifies machine maintenance, which in turn saves them valuable time and money. It’s also a significant advantage for REFORM’s business, as they’re able to save on the cost of providing field technicians.
For more information on Maintenance expertise, built in talk to Bosch Rexroth Limited
Enquire Now
List your company on FindTheNeedle.