
Sign In
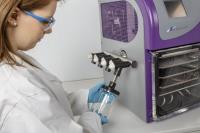
Freeze Drying vs Spray Drying: is it essentially quality vs cost?
In an increasingly demanding industry when it comes to productivity and profitability, sometimes hard decisions need to be made as can be seen in the debate relating to the usage of freeze drying or spray drying when developing a product process, and it can come down to something as cut and dry as costing overheads. We have therefore played a bit of ‘devils’s advocate’ when considering the benefits of both to help you choose which is best for your project and product.
Which Should You Choose?
Freeze drying is widely recognised in the biopharmaceutical industry as the preferred method Advantage-021 (Medium) (2)for preserving a wide range of pharmaceutical formulations when stability in the liquid state is inadequate, storage requirements are too stringent, or a solid form of the product is desired.
Whilst freeze drying is certainly the established drying process across a variety of materials, ranging in sensitivity levels, due to the costs, and sometimes volumes associated with the technique, research has also been undertaken to investigate alternative methods, such as spray drying.
Although relatively new to the industry, spray drying does come with some benefits such as capability to work with higher throughput (more continuous rather than batch), amounts in a scalable manner -making it a viable option to lyophilisation, but only in certain situations.
The Drying Process
The principle of freeze drying involves the initial freezing of a product, usually in a controlled manner to manipulate the ice crystal structure, which thereafter is placed in a vacuum where sublimation (or primary drying) takes place in order to remove the unbound water.
Next comes secondary drying to sublime the bound water, taking the material down to a user defined residual moisture level. Given the target at this stage is bound rather than unbound/free water more energy is required to drive the process by raising shelf temperatures to +20°C or above, coupled with a low atmospheric pressure, causing ice to turn directly in to water vapour (by passing the liquid phase).
Subject to the nature of the sample being dried on a given lyophilisation cycle, the delicate balance between temperature and vacuum is vital to ensure that a successful batch with no impact on product efficacy, is produced post drying. To achieve this, certain products may need to undergo freeze drying conditions ranging from 12 hours to 5 days, based on their inherent sample properties.
Spray dDropping-Powder-1-iStock_000013005520_Small-2-203x300rying is considered to be a more simple (and faster) process, involving the conversion of a liquid formulation into a dry powder in one single step. The solution is atomised into fine droplets which are quickly dried straight after in a large chamber using warm gas. The resulting dry particles are then collected with a cyclone.
Although faster, and less expensive than freeze drying, one of the significant downfalls tends to be due to the high processing temperatures/ shear forces it demands, these of course, are what many customers seek to avoid in the stringently controlled pharma/ bio-tech industries.
Product temperatures in freeze drying are generally below 0°C in primary drying and 20-30°C during secondary drying, whereas product temperatures in spray drying are regularly above 80°C.
The direct impact of working with these higher (80°C) temperatures, will sometimes be an overall loss of sample quality post drying in terms of inherent product characteristics:
Efficacy
Taste
Smell/colour
Nutritional value i.e. nutrients in food products
Biological yield – greater level of log reduction of cells i.e. bacterial
Proteins degeneration
Use in the Industry
Both processes can be used for a vast range of applications. For example, freeze drying is typicvarious-product-formatsally sought out for the preservation of different cell types, fine chemicals/ laboratory reagents, injectable vaccines, as well as food industry & dairy products. Because it is typically performed with product directly filled in vials or other containers, this processing method is best suited for formulations that do not require further processing after drying; additionally, vials can be sealed in-situ of the lyophiliser, thus avoiding potential contamination when the cycle is complete.
Spray drying, on the other hand, is more commonly associated with bulk rather than vial based processing. However, it is a common misconception that spray drying is only a suitable process for food and robust bulk pharmaceuticals, where contemporary research suggests it may be a valid methodology for use with some complex products i.e. microencapsulated bacteria and nanoparticulates, for example.
Efficiency, Quality and Cost
It is widely accepted the costs associated with spray drying are less than those of of freeze drying, which has made the technique one of interest for certain markets; and, being more open to larger throughput potentials, spray drying can be deemed a ‘continuous process’, unlike the batch format associated with freeze drying.
Nonetheless, it is important to consider that, although spray drying is usually less in ‘upfront cost’, this isn’t always the case for more complicated formulations. Products that require multiple coating layers will need to undergo multiple coating processes, which in turn can be very time consuming and cost prohibitive, making a simpler formulation that is freeze dried a more cost effective solution.
Moreover, it is the robust quality of product where freeze drying’s strength lies. Accurate control of low processing temperatures minimises any risk of intrinsic products properties, such as collapse, eutectic melt, or glass transition temperatures being exceeded, making freeze dried products of the highest of quality. The shear stress biopharmaceuticals can be exposed to during spray drying, combined with the required high processing temperatures can destabalise compounds such as proteins and damage product properties, which, studies have shown, ultimately diminishes product quality.
Biopharma Group has been in business for nearly 30 years, with its core area of expertise in the drying technology fields, maintaining an analytical laboratory (that houses both freeze and spray drying instrumentation at the R&D scale) at our UK facility. This allows for us to perform unbiased comparisons between both techniques, for your reference to support the development of your product.
If you would like to discover more about how Biopharma can assist your product and/ or cycle development projects, please contact us at btl@biopharma.co.uk or +44 (0)1962 841092
For more information on Freeze Drying vs Spray Drying: is it essentially quality vs cost? talk to Biopharma Group
Enquire Now
More News
List your company on FindTheNeedle.