
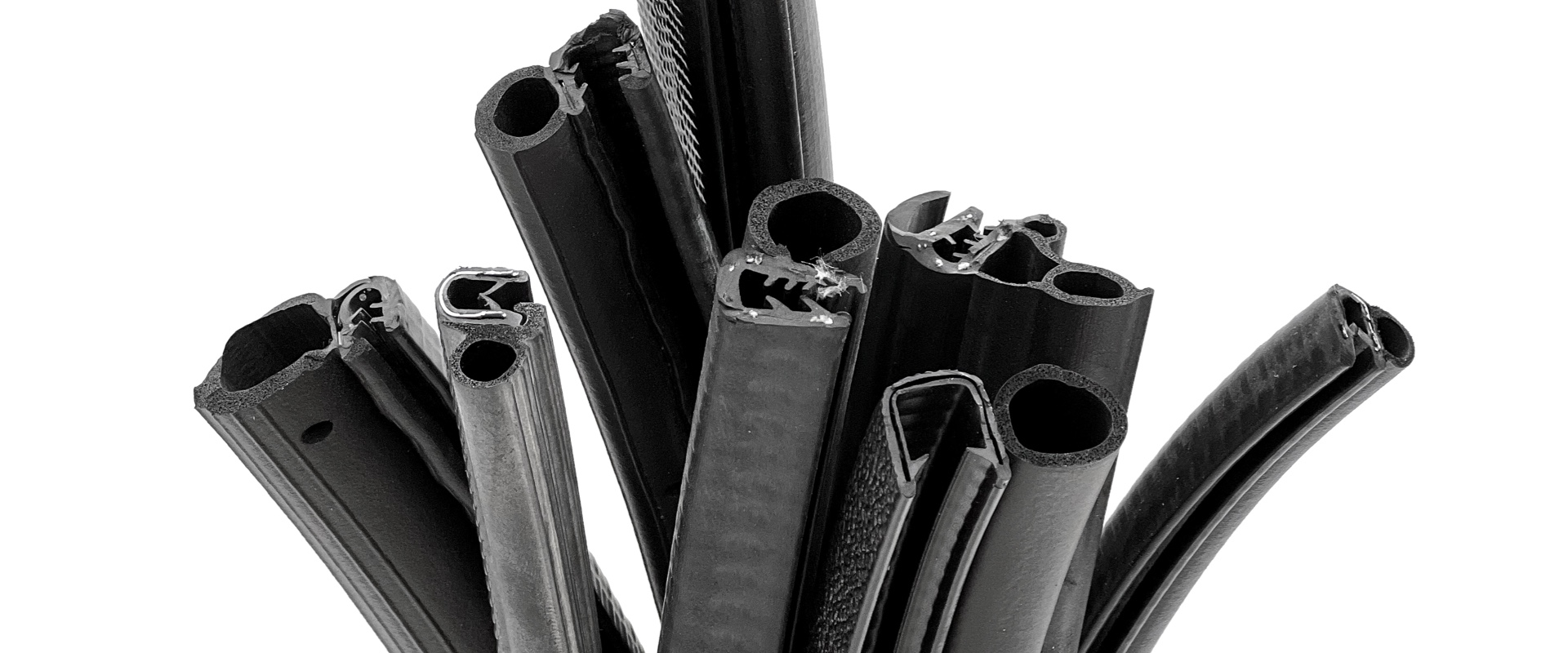
Extruded and co-extruded rubber seals are used in various industrial and commercial applications, both serving the primary function of providing an effective sealing solution. Although they may seem similar at a glance, these two types of seals have distinct differences in their manufacturing processes, material properties, performance characteristics and cost implications. Their individual applications make them suitable for different uses.
Extruded and Co-Extruded Rubber Seals
Manufacturing Process
Rubber extrusions are manufactured using a fairly standard extrusion process where a single type of rubber is fed into an extruder. This compound is then heated and forced through a die that shapes the material to the desired profile shape. This continuous profile is then vulcanised or cured, setting its shape and enhancing the properties of the rubber compound. Whilst this is a simplified overview of the extrusion process, it accurately demonstrates the process of extruding a rubber seal using a single material.
Co-extruded rubber seals require a more complex manufacturing process which involves simultaneously extruding two or more different types of rubber compounds. These materials are individually fed into multiple extruders and then combined in a single die to form a composite profile. The result is a seal that incorporates different layers or sections, each with different material properties, hardnesses and colours. This complexity allows for the creation of seals with varied functionalities within the same profile.
Material Performance Characteristics
The materials used to extrude rubber seals are typically standard rubber compounds such as EPDM, neoprene, silicone or nitrile. The result of using one material limits the properties of the seal to those of the material that it was made from. This means that each seal can only exhibit the characteristics inherent to its material, such as temperature resistance, flexibility, or chemical resistance. For example, a seal made from nitrile will have good oil resistance, whereas one made from silicone will perform well in high-temperature environments.
The consistency in material properties throughout the seal makes it ideal for applications that require uniform performance.
By combining multiple materials, co-extruded seals can feature, for example, a rigid foot with a flexible compressible sealing bulb. It is also possible to extrude a combination of rubber and other materials, such as PVC. This allows for a level of customisation and adaptability in performance that is not achievable with standard sections extruded from one material.
This blend of materials allows for more complex applications where diverse characteristics are required in a single seal, like combining high-temperature resistance with excellent compression set resistance. These sections can be custom-designed to offer different functionalities in various sections of the seal. Such versatility is essential for applications that require seals to perform multiple roles, such as providing both a rigid mounting point and a flexible sealing surface.
Applications and Uses
Extruded rubber seals are manufactured using a fairly standard extrusion process where a single type of rubber is fed into an extruder. This compound is then heated and forced through a die that shapes the material to the desired profile shape. This continuous profile is then vulcanised or cured, setting its shape and enhancing the properties of the rubber compound. Whilst this is a simplified overview of the extrusion process, it accurately demonstrates the process of extruding a rubber seal using a single material.
Co-extruded rubber seals require a more complex manufacturing process which involves simultaneously extruding two or more different types of rubber compounds. These materials are individually fed into multiple extruders and then combined in a single die to form a composite profile. The result is a seal that incorporates different layers or sections, each with different material properties, hardnesses and colours. This complexity allows for the creation of seals with varied functionalities within the same profile.
Cost and Manufacturing Complexity
Extruded sections are generally less expensive due to the simpler manufacturing process and use of a single material. As these extrusions only require one machine, this simplicity translates to lower production costs. This makes extruded seals a cost-effective option for many standard applications.
This compares to co-extruded rubber products which are usually more expensive to manufacture. The increased cost is a result of the more complex co-extrusion process, which requires precise control of multiple extruders and the flow of different materials. The use of multiple materials further adds to the cost, often requiring a larger minimum order quantity. Despite the higher price point, the enhanced functionality and customisation offered by co-extruded seals often justify their cost in demanding applications.
Durability and Longevity
The durability of extruded rubber seals depends solely on the properties of the material used. If the material is correctly chosen for the application environment, these seals can offer good longevity. However, they might not perform as well in environments that require a combination of properties that no single material can provide.
Co-extruded rubber seals, in contrast, offer enhanced durability by combining materials that can provide superior resistance to wear, UV light or chemical exposure. This engineering flexibility often leads to longer-lasting seals, as they can be specifically designed to withstand the unique challenges of the environment in which they will be used.
Should I Use Extruded or Co-Extruded Rubber Seals?
The choice between extruded and co-extruded rubber seals hinges on the specific requirements of the application. Extruded sections offer simplicity and cost-effectiveness, often with significantly lower minimum order quantities. For applications with uniform requirements, these profiles offer a reliable sealing solution to most industries. However, co-extruded seals exhibit enhanced performance characteristics that provide tailored solutions for more complex or demanding environments. Understanding these key differences is essential to select the appropriate type of seal for their specific needs.
At Seals Direct, our expert team has extensive experience in understanding our customers’ requirements and recommending the best profile. We can discuss the factors that influence the choice of rubber seal and explore custom rubber sealing solutions or off-the-shelf products. Please contact us to discuss your requirements.
For more information on What Is the Difference Between Extruded and Co-Extruded Rubber Seals? talk to Seals Direct Ltd